Healthcare environments pose unique challenges to worker safety. From infectious pathogens to hazardous chemicals, healthcare workers face exposure to numerous risks on a daily basis. Personal protective equipment (PPE) is designed to protect healthcare staff by minimizing contact with workplace hazards.
The Occupational Safety and Health Administration (OSHA) has established standards to ensure healthcare workers protect themselves properly with the right PPE. This guide from Gamma Compliance Solutions will explore the essential OSHA PPE rules healthcare staff must follow, including guidelines for items such as gloves, masks, eye protection, protective clothing, and more.
You’ll also find training requirements and recommendations to ensure compliance. By adhering to OSHA’s standards and training requirements, healthcare facilities can reduce workplace injuries and improve overall safety.
Importance of Following OSHA PPE Rules
Personal protective equipment maintains the safety and well-being of healthcare professionals. OSHA’s regulations address the critical aspects of PPE to ensure workers stay protected from biological and physical hazards. Failure to follow these rules can lead to severe consequences, including contamination risks, workplace accidents, and legal repercussions for non-compliance.
OSHA mandates specific requirements for each type of PPE used in healthcare settings. Healthcare employers must provide proper fitting PPE to employees at no cost. Through comprehensive training, workers can understand the correct use and limitations of PPE to promote workplace safety.
Gloves: Types, Proper Use, and Disposal
Gloves are one of the most common pieces of PPE across all healthcare sectors. They protect against exposure to bloodborne pathogens, infectious agents, and hazardous chemicals.
Different types of gloves suit specific tasks. For instance, nitrile gloves are resistant to chemicals and provide durability, while latex gloves offer a barrier with elasticity and tactile sensitivity.
Healthcare workers must select gloves that fit snugly without causing discomfort. They must wear gloves during patient care and when handling potentially contaminated materials. After use, workers should carefully remove gloves to prevent contact with the contaminated surface. OSHA emphasizes that workers must discard their gloves immediately after each use and never reuse them.
Facilities must also ensure safe disposal methods for used gloves. Workers should dispose of them in approved biohazard containers to minimize the risk of cross-contamination and exposure.
Masks & Respirators: Selection, Fitting, and Maintenance
Masks and respirators protect healthcare staff from airborne contaminants and respiratory hazards. Basic surgical masks are used to prevent the spread of droplets during procedures, while respirators, such as N95 masks, offer higher levels of filtration for airborne pathogens.
OSHA requires a proper fit for respirators to ensure their effectiveness. Before an employee uses a respirator for the first time, teams must conduct a test to ensure a proper fit. Additionally, healthcare workers must perform daily fit checks to confirm that the mask seals tightly against the face.
Regular maintenance of masks and respirators is also vital. Disposable masks, such as N95s, require replacement after each use or when damaged, while staff should clean and store reusable respirators according to the manufacturer's recommendations. Healthcare employers must provide clear guidance on when to replace or sterilize equipment.
Eye Protection: Goggles and Face Shields for Different Hazards
Eye protection is essential for shielding healthcare workers from chemical splashes, infectious droplets, and physical hazards. OSHA standards require staff to use goggles or face shields in situations where eyes may be at risk. Goggles provide a secure fit, enveloping the eyes completely, whereas face shields cover the entire face and provide broader protection.
The right type of eye protection depends on the specific hazard. For example, goggles are ideal for applications involving splashes of chemicals or infectious liquids, while face shields are more suitable for high-risk surgical procedures. Eye protection gear must fit comfortably and not obstruct vision. They should also be compatible with other PPE, such as respirators.
Eyewear requires regular maintenance to provide continued protection. OSHA advises regular cleaning of goggles and face shields with disinfectant wipes. Inspect this equipment regularly to look for signs of damage such as cracks or scratches that could compromise safety.
Protective Clothing: Gowns and Coveralls for Infection Control
Protective clothing plays a crucial role in infection control, serving as a barrier between healthcare workers and potentially infectious materials. OSHA identifies various types of protective clothing, including isolation gowns, coveralls, and aprons.
Selecting the appropriate protective clothing depends on the task at hand. Isolation gowns are common for patient care in high-risk areas, while workers often wear splash-resistant coveralls when working in labs handling hazardous chemicals. Protective clothing must cover all exposed skin and fit securely.
Proper use and disposal are equally important. Safely discard disposable gowns after use and launder reusable coveralls following OSHA-standard disinfection protocols. Employers must provide protective clothing that complies with safety standards and train employees on its correct use.
Additional PPE Tools for Specialized Hazards
While gloves, masks, eye protection, and gowns cover the most common risks, workplaces may require additional PPE for specialized hazards in healthcare settings. OSHA standards also address situations involving hearing protection, heat resistance, and chemical exposure.
Hearing protection such as earplugs or earmuffs may be necessary in noisy environments where exposure exceeds OSHA’s permissible noise levels. Heat-resistant gloves or aprons protect against thermal burns during laboratory procedures. Chemical-resistant materials, including specialized respirators or protective suits, safeguard workers handling hazardous substances.
Employers will select each tool based on their conducted hazard assessment. Always dispose of these tools in designated areas to ensure ongoing safety and compliance.
Training Requirements for PPE Use
OSHA mandates comprehensive training programs to ensure proper PPE use in healthcare settings. Training equips workers with the knowledge to select, use, and maintain their PPE effectively, reducing the likelihood of workplace injuries and exposure.
Training topics must include the appropriate selection for various situations, proper donning and doffing techniques, and PPE limitations and how to account for them. OSHA requires hands-on training, ensuring workers become familiar with their gear. Employers must also provide regular refresher courses and update employees on new safety standards.
Gamma Compliance Solutions offers OSHA-compliant PPE training specifically designed for healthcare facilities. Our expert-crafted programs and OSHA manuals for medical office use provide workers with the skills and confidence to adhere to safety standards. Healthcare organizations can rely on these training solutions to maintain compliance and foster a culture of safety.
Ensuring Healthcare Safety Through Proper PPE Practices
PPE is a vital component of workplace safety for healthcare staff. From gloves and masks to protective clothing and eye shields, each element plays a unique part in reducing risks and protecting workers. To meet OSHA standards, healthcare facilities must follow these rules on proper use, disposal, and training for all PPE.
To learn more about OSHA-compliant PPE training, visit Gamma Compliance Solutions. Our tailored programs provide healthcare organizations with the resources they need to enhance safety and adhere to industry standards.
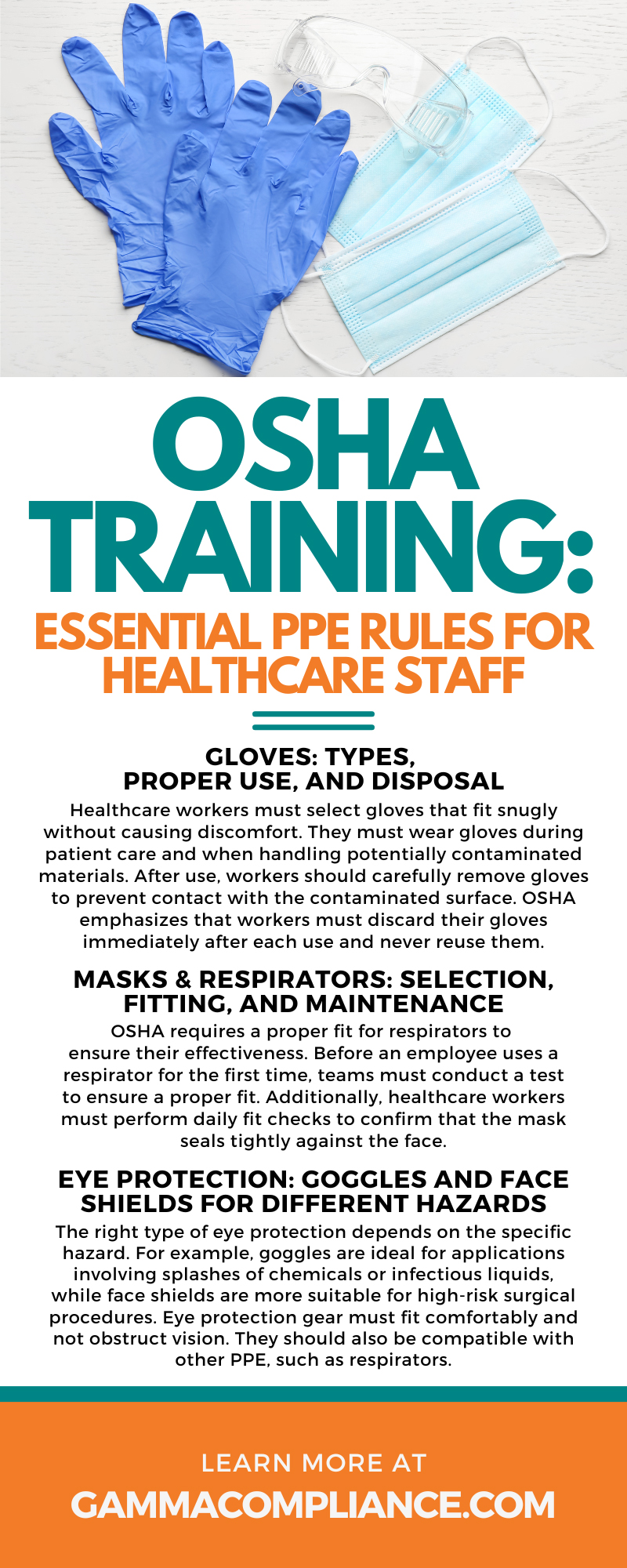
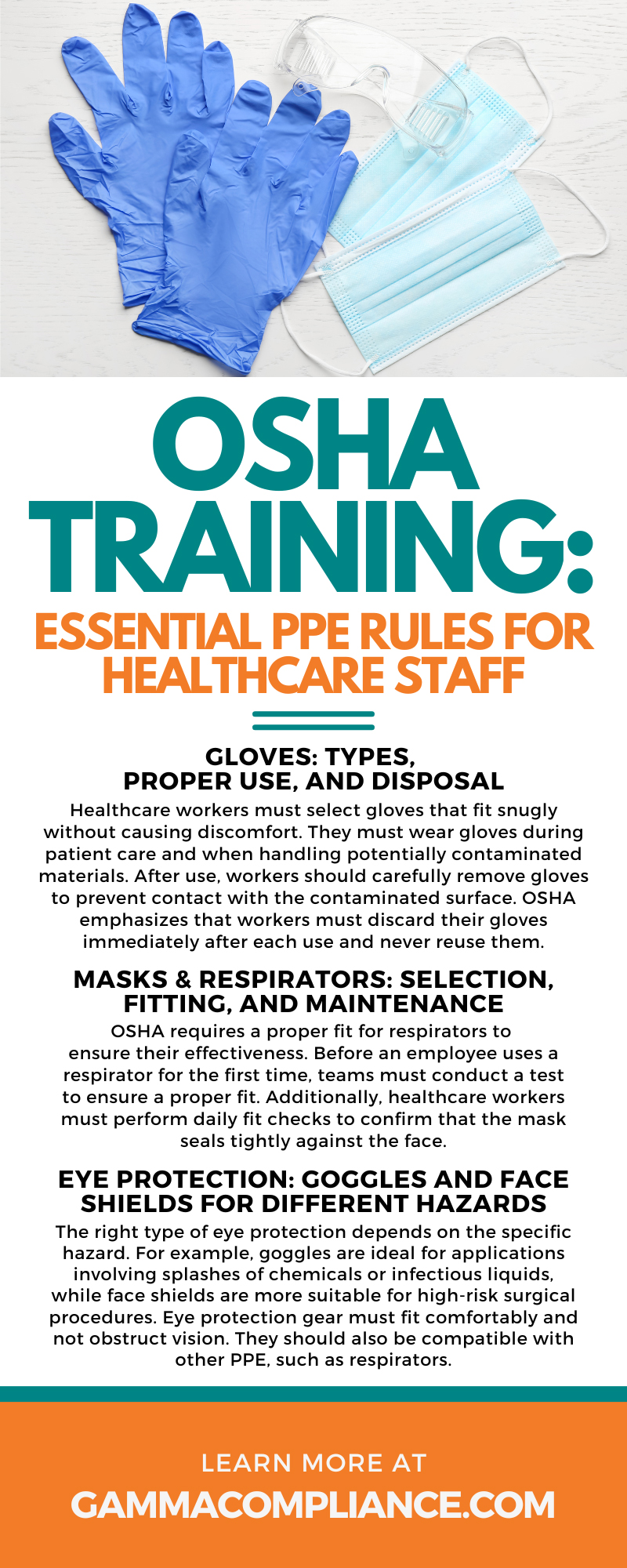