Business owners, healthcare practitioners, and HR managers must understand and implement Occupational Safety and Health Administration (OSHA) standards to maintain a successful work environment. These regulations are designed to ensure a safe and healthy workplace for all employees. This guide from Gamma Compliance Solutions will walk you through the essential steps to properly implement OSHA standards to ensure compliance and safeguard your team.
Understanding OSHA Standards
OSHA standards are federal regulations that mandate safe working conditions. They cover various concepts, such as equipment safety, hazardous materials, and employee training. Compliance with OSHA standards is a legal requirement and a moral obligation to protect your employees.
Knowing these standards helps you create a safer work environment. It also reduces the likelihood of accidents and legal issues. Familiarizing yourself with OSHA guidelines is the first step toward compliance.
OSHA standards undergo regular updates, so it’s crucial to stay informed. Subscribe to OSHA newsletters and regularly complete safety training to stay informed of policy changes.
Consequences of Improper Implementation
Failing to implement OSHA standards correctly can have severe repercussions. Non-compliance can result in hefty fines and legal actions against your business. Beyond financial penalties, your company’s reputation could suffer.
Employees working in unsafe conditions are at higher risk of injuries, which can lead to increased workers’ compensation claims and higher insurance premiums. Additionally, workplace accidents can cause operational disruptions and lost productivity. Worker injuries can cause employees and customers to lose trust in your facility, leading to the loss of workers and clients.
Properly implementing OSHA standards is critical for maintaining a safe and efficient workplace. It also demonstrates your commitment to employee welfare and regulatory compliance.
How To Implement OSHA Standards Correctly
Implementing OSHA standards correctly involves several steps. First, familiarize yourself with the specific standards relevant to your industry. OSHA provides industry-specific guidelines to help you understand what applies to your workplace.
Next, develop a comprehensive safety plan. This plan should outline procedures, responsibilities, and resources needed for compliance. Your plan should be accessible and easy to communicate to your employees.
Finally, integrate safety practices into your daily operations. Regularly review and update your safety plan to reflect any changes in OSHA standards or your workplace environment.
Below are some specific tips and strategies for implementing OSHA standards in your facility.
Educate All Levels of Employment on OSHA Standards
Education is key to effective OSHA compliance. Train managers, supervisors, and all employees on the importance of OSHA standards and their role in maintaining a safe workplace. Use a combination of training methods, including workshops, online courses, and hands-on demonstrations.
OSHA and HIPAA compliance training should be an ongoing occurrence. Schedule regular refresher courses to keep safety practices top-of-mind. Employees should feel confident in their ability to identify and address potential hazards.
Post OSHA Information in Your Facility
OSHA information accessibility is also important. Post OSHA flyers and notices in prominent areas of your facility. This ensures that all employees keep these standards in mind throughout their days.
Don't forget to remove outdated materials and replace them with current information. Regularly update your postings. Whenever there are changes to OSHA standards or company policies, reflect the new information in your postings. This practice helps maintain compliance and keeps safety information readily available.
Evaluate Your Workplace
Conducting a thorough evaluation of your workplace is crucial for OSHA compliance. Identify potential hazards and assess your current safety measures and their effectiveness. Use OSHA’s self-inspection checklists as a guide.
Involve employees in the evaluation process. They can provide insights into potential risks and areas for improvement. Their participation also fosters a sense of ownership and responsibility for workplace safety.
Document your findings and develop a plan to address the issues you identify. Regular evaluations help ensure ongoing compliance and continuous improvement.
Minimize Workplace Hazards
Proactively minimize workplace hazards. Implement engineering controls, administrative controls, and personal protective equipment (PPE) to reduce risks. Engineering controls involve modifying equipment or processes to eliminate hazards. Administrative controls are policies and procedures designed to minimize risks. Ensure employees follow safety protocols and receive regular training. PPE provides an additional layer of protection against potential hazards.
Regularly review and update your hazard control measures. Stay informed about new technologies and best practices to enhance workplace safety and minimize hazards in your facility.
Have a Reporting System
A robust reporting system is crucial for identifying and addressing safety issues. Encourage employees to promptly report hazards, near misses, and accidents. The reporting process should be simple and accessible to encourage employees to use it.
Respond to reports quickly. Investigate the root cause of reported issues and implement corrective actions. Keep employees informed about the steps you’ve taken or how you plan to address their concerns.
Analyze reported data to identify trends and areas for improvement. You can use this information to enhance your safety program and prevent future incidents.
Keep Record of Injuries and Accidents
Maintaining accurate records of injuries and accidents is a legal requirement for businesses. It also helps you identify patterns and areas for improvement. Keep detailed records of all incidents, including the nature of the injury, the circumstances, and the steps you take to address the issue.
Use OSHA’s recordkeeping forms to ensure compliance. Regularly review your records to identify trends and potential hazards. Use this information in conjunction with employee reports to improve your facility’s safety and programs.
Finally, share your findings with employees. Transparency fosters trust and encourages a culture of safety.
Tips for Practicing Ongoing Compliance
Ongoing compliance requires continuous effort. Stay informed about changes to OSHA standards and update your safety plan accordingly. Regularly review and refine your safety procedures to reflect best practices.
Engage employees in the compliance process. Encourage their participation in safety training, inspections, and reporting. This fosters a culture where safety is a shared responsibility.
Utilize resources provided by OSHA and other industry organizations. You can easily find OSHA resources and training courses through Gamma Compliance Solutions. We provide up-to-date OSHA and HIPAA training materials for healthcare facilities across the country. Browse our resources today if you’re looking for ways to implement OSHA standards in your facility.
Implementing OSHA standards is essential for maintaining a safe and compliant workplace. It protects your employees, enhances productivity, and safeguards your business from legal and financial risks. By following the steps above, you can create a robust safety program that ensures ongoing compliance.
For comprehensive OSHA and HIPAA compliance training courses, explore Gamma Compliance Solutions. Empower your team with the necessary knowledge and tools to maintain a safe and compliant workplace.
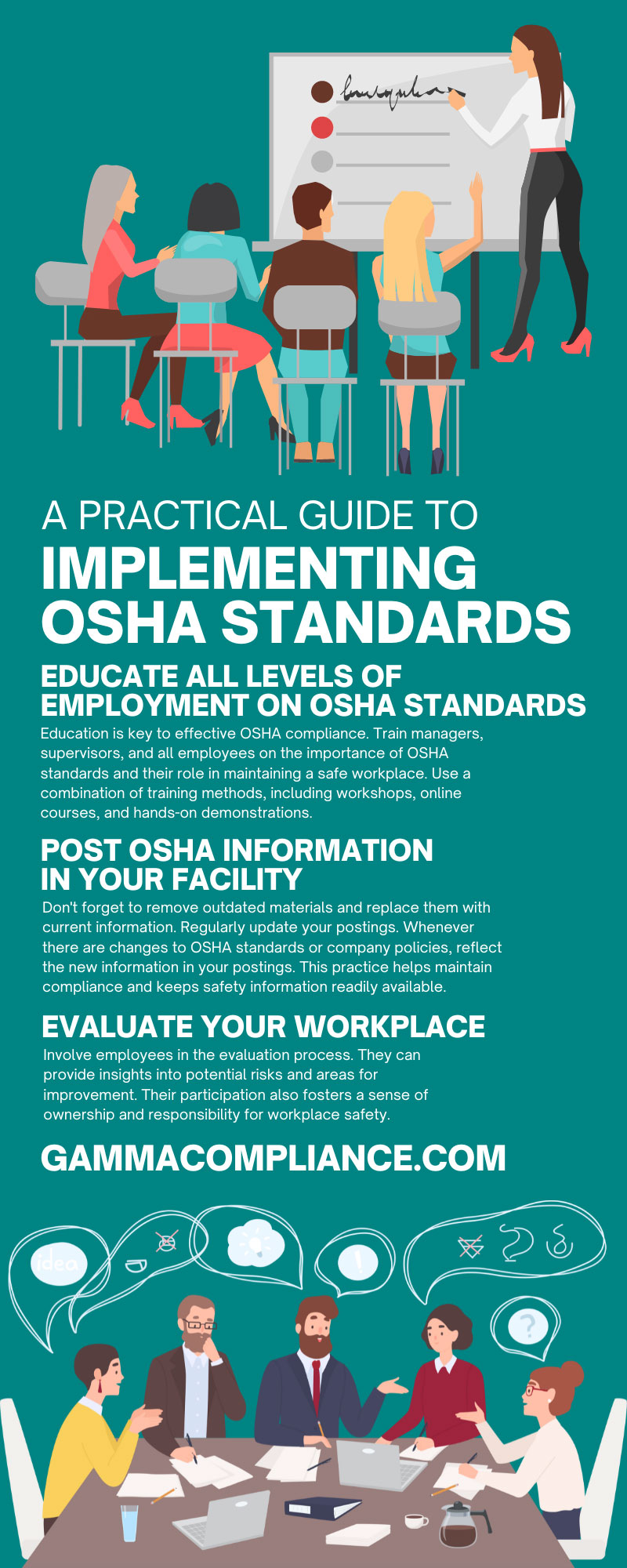
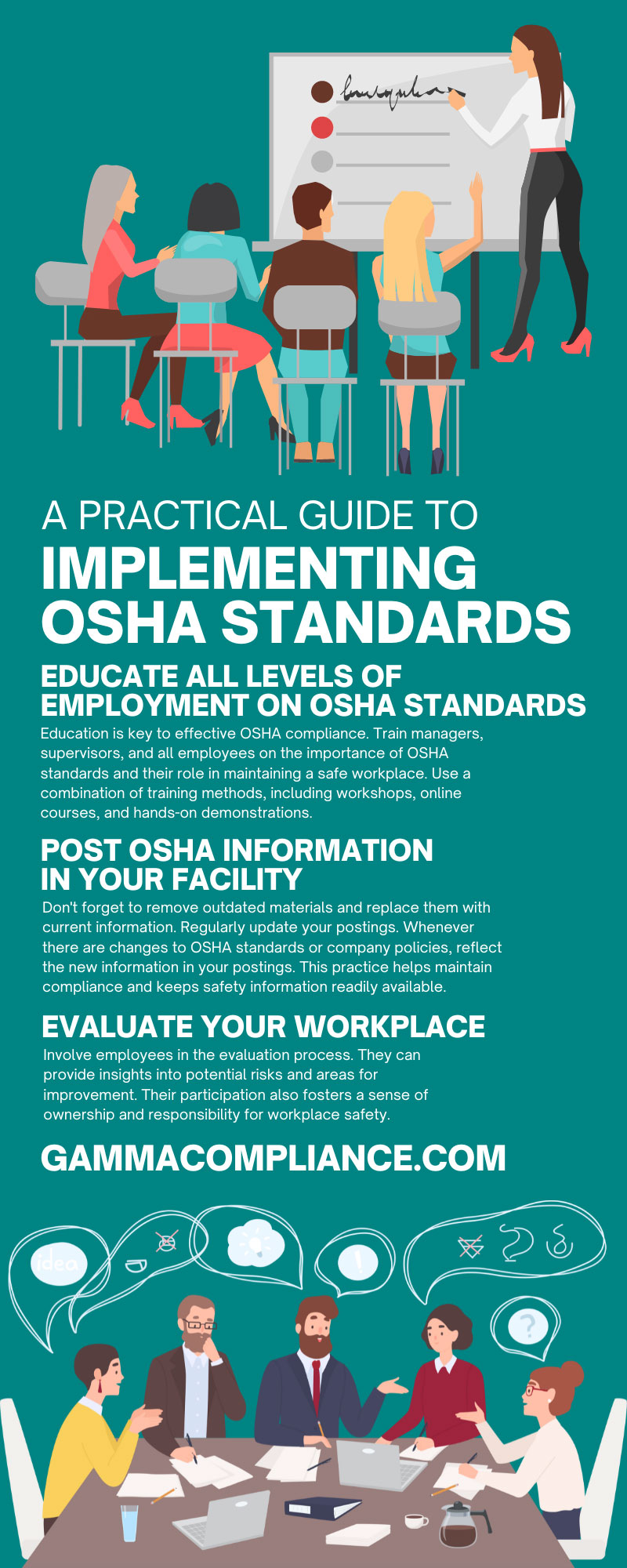